<![CDATA[On October 7th 1913, an industrial revolution hit the American Automotive Industry that would have far reaching effects around the world. For the first time, the Ford motor company's cars were produced on a moving assembly line. Going forward, the event would have a remarkable impact on the productivity of the automobile industry, which in turn allowed cars to become much more affordable for 'normal Americans'. The innovation was installed in Henry T. Ford's Highland Park automobile factory in Michigan. The new moving assembly line became the focus of the entire plant, as all parts in the process of construction were sequenced along a conveyor belt. The construction of the chassis for Model T's was done by pulling the frame through the factory using a motor and rope. As the chassis moved through the factory, it would stop at various workers, allowing a stage in the construction process to be completed before the car moved on. Immediately, the moving assembly line more than halved the construction time of a single Model T Ford from twelve and a half hours, to six. A year later, the construction time for a complete car had dropped to ninety three minutes. The impact of this time saving method came to be almost as significant as the Model T itself. It signalled an industrial revolution in US manufacturing, and within a few years the technique was used for the construction of everything from food to weapons. The moving assembly line was exported throughout the world as the most effective way to achieve mass production, and the increased capacity it offered became fundamental in the Allied Victory in the Second World War. Assembly line technology was not Ford's invention, but he was responsible for realising the enormous potential it offered. The direct inspiration was the industrialised slaughterhouses and meat packing plants in nineteenth century Chicago and Cincinnati. In these plants, the actions from slaughtering an animal to packing its meat were all performed along a rail which carried the carcass through the process. The Highland Park factory experimented with the technique in the construction of fly wheel magnetos. Instead of one worker constructing the entire magneto, it was divided into twenty nine smaller procedures. The magneto was moved along the plant, which each worker completing one of the steps in the production. The successes of this initial trial in early 1913 inspired its adoption throughout the construction process. The revolution in industrial processes was remarkable for the opportunities it opened up to working class Americans. Automobiles had been around for years before the arrival of the Model T, but their cost meant they were only available to the wealthiest members of society. Henry Ford had always stated his desire to make a car that was affordable for every American. Before the implementation of the moving assembly line, this was still not possible because the costs of production were too high, meaning the automobile remained a middle and upper class luxury. The assembly line reduced production costs so much that by 1916 a Model T cost less than $300, and sales of the car had tripled since 1912. As mentioned above, moving assembly lines had existed before they were utilised at Highland Park. The Ford motor company was responsible for understanding the huge potential they contained. Their implementation in Michigan in October 1913 was paramount in the democratisation of car ownership, and the triumph of American manufacturing in the middle of the twentieth century. ]]>
Ford Moves Ahead of the Times
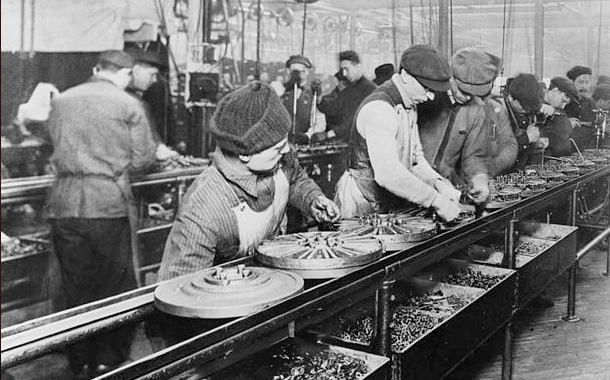